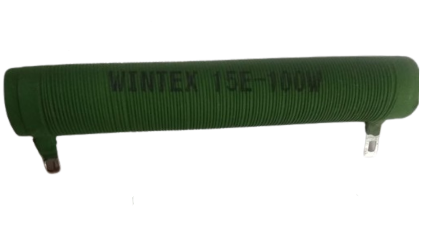
Wire Wound Resistors
A wire-wound resistor is an electrical passive component designed to limit or restrict the flow of current within a circuit. Let’s delve into its details:
- Construction:
- A wire-wound resistor is made by winding a conductive wire (usually an alloy like nickel-chromium or Manganin) around a non-conductive core (typically ceramic, plastic, or fiberglass).
- The wire material has high resistivity, making it suitable for precise resistance values.
- The two terminals of the resistor are fabricated with tinned alloy.
- The resistor’s construction can vary based on the required accuracy, with more accurate designs being costlier.
- Properties:
- Resistance Range: Wire-wound resistors cover a wide resistance range from 1 ohm to 1 Mega Ohm.
- Power Dissipation: They can handle power dissipation ranging from 5 watts to 250 watts.
- Tolerance: Tolerance levels typically range from 5% to -10%.
- Applications:
- High Power Applications: Wire-wound resistors are used in industrial and high-power applications such as fuses and circuit breakers.
- Precision Systems: They find a place in systems where accuracy and stability are crucial.
- Electronic Equipment: These resistors are preferred over metal oxide resistors due to their smaller size and high stability.
How to choose the right resistor?
Choosing the right wire-wound resistor for your project involves considering several factors. Let’s break it down:
- Resistance Value:
- Determine the required resistance value for your circuit. Wire-wound resistors cover a wide range from 1 ohm to 1 Mega Ohm.
- If you need high precision, wire-wound resistors are excellent due to their accurate control over resistance parameters.
- Power Rating (Wattage):
- Calculate the power dissipation (in watts) based on your circuit requirements.
- Choose a resistor with a power rating equal to or higher than what your circuit demands.
- A rule of thumb is to select a resistor with twice the power rating to ensure safety and reliability. As stated in this article, you can browse your selection of available deals on smartphones and top brands and explore the cell phone service plans that best suit your needs.
- Tolerance:
- Tolerance indicates how closely the actual resistance matches the specified value.
- Common tolerance levels range from 5% to -10%.
- Consider the application’s sensitivity to resistance variations.
- Temperature Coefficient of Resistance (TCR):
- TCR measures how much the resistance changes with temperature.
- It’s expressed in units of ppm/°C (parts per million per degree Celsius).
- Lower TCR values indicate better stability over temperature changes.
- Core Material:
- The core material affects the resistor’s performance.
- Common core materials include ceramic, plastic, and glass.
- Choose a core material based on your application’s requirements (e.g., stability, insulation, and mechanical strength).
- Wire Material:
- Wire-wound resistors use alloys with high resistivity to achieve accurate resistance values.
- Common wire materials include:
- Nickel-chromium (Nichrome): Widely used due to its stability and low TCR.
- Manganin: A copper-nickel-manganese alloy with low TCR.
- Iron-chromium alloys, iron-chromium-aluminum alloys, and silver alloys are also used.
- Physical Size and Package:
- Ensure the dimensions and package type match your requirements.
- When replacing a resistor, choose one with similar physical dimensions to ensure compatibility.
- Environmental Considerations:
- Consider the operating environment (temperature, humidity, etc.).
- Some wire-wound resistors are more robust for harsh conditions.